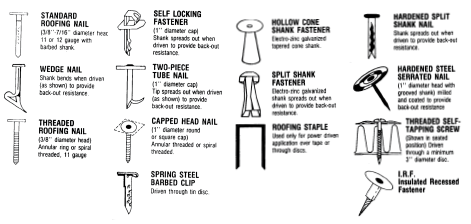
The most commonly used item for fastening wood is the nail. Nails and spikes come in a variety of lengths, diameters, heads, points and shank styles. Knowing what to look for enables a craftsperson to choose the best type of fastener for each particular job.
Nails come in lengths from 9.5 mm to 150 mm (3/8 in to 6 in), and spikes are 100 mm to 350 mm (4 in to 14 in). Diameters and patterns vary according to function.
In Canada, nails are specified by the length and diameter of wire used in manufacture. In the United States, the “penny” system of specifying nail sizes is also used. This system is often confusing since a particular “penny” size may refer to as many as four different lengths and diameters.
When a nail is driven, wood fibres are bent down or are broken off and jammed between the nail and other unbroken fibres. Most of the withdrawal resistance of a nail in wood results from this jamming and wedging action. Other fibres, forced aside as the nail enters the wood, exert a squeezing action thus increasing the friction between the nail and the wood. The same principle applies to concrete fasteners. In this case, by nailing concrete nails, or drilling a hole for the nail, a fine concrete dust is created on the sides of the hole. When the fastener, if sized right, is engaged in the hole, the forces of compression and friction hold it in place.
In the case of wood, because the shape and texture of the nail shank affects the degree of wood fibre distortion, the design of the nail shank affects the strength of a nailed joint.
Various coatings and shank deformations have been devised to increase nail friction in wood. The “Ardox” type spiral shank nail, manufactured from helically deformed wire, gives improved holding power. Sharp-crested annular or helical threads, produced by roll-threading a round nail, give maximum holding power. Resin or shellac type coating; increased holding power.
Nails are made with many different heads and points. Each is designed for a specific purpose. Flat heads are used in general construction, while countersunk heads are used where concealment of the nail head is desirable.
Various effects can be achieved using nails with round, oval, or pointed heads. Special nails have been developed for particular applications, such as fastening roofing or drywall.
By far the most widely-used nail point is the medium diamond. The medium diamond point is a compromise between a brig, sharp point, for easy driving and good holding power and a short-blunt point for reduced splitting of the wood.
Nail Types
Nails are sized according to their length and gauge. Common nails and spikes have a heavy gauge. Wire or box nails and finish nails are slender. Most of the nail types below may be purchased with zinc or aluminium coatings designed to provide increased corrosion resistance.
- Common Nails have a medium-sized head, and are smooth steel. Sometimes called “brights” because they are shiny. They have fair holding power but may split wood because of their thickness.
- Wire Nails are most commonly found as a “coated” nail (phosphate coating). This grey slender nail, with the chalky finish has extremely good holding power, but may be hard to drive in hard woods since it may bend.
- Ardox Nails are a heavy gauge nail with a four-sided spiral that increases the holding power greatly. They are also available with phosphate coating.
- Finish Nails are bright, slender and have small heads. The head is sunk below the surface of the wood by a distance equal to its own width and the hole is usually filled to hide the metal.
- Roofing Nails are used to fasten shingles and felts to nailable wood decks. They may be hand driven or power driven. They should have a minimum 12-gauge shank diameter (3 mm (1/8 in)) and a head of a minimum of 9.5 mm (3/8 in)). Nails may be smooth shank, but deformed shanks have greater holding power.
Steel nails must have adequate corrosion protection. Bulk nails are usually hot-dipped galvanized while coils are chromate-treated.
All nails must be of sufficient length to penetrate into the roof deck a minimum of 19 mm (3/4 in). In the case where the deck is less than 19 mm (3/4 in) thick, they must penetrate through the deck.
Special Nails
Where corrosion may reduce nail life or cause staining or marring of a finished wood surface, nails of corrosion-resistant metals are necessary. In such cases, coated or plated steel, aluminum, or copper nails are used. Nails of brass, bronze, stainless steel and monel metal can be had on special order.
Double-headed nails are used for scaffolding, concrete formwork and other temporary construction. They are driven into the lower head, leaving the upper head exposed for easy withdrawal and to prevent damage to lumber.
Nailing Tips
- Be sure to use the proper nail for the job.
- Two or three sharp taps, not blows, will help to start nails more easily.
- Keep the face of your hammer clean.
- Avoid hitting it against brick or concrete.
- If the head of the hammer becomes loose, remove the handle, trim and refit the wedge.
- When pulling nails, a small wooden block under the hammer will improve leverage and protect the wood’s surface.
- When driving nails, keep your eye on the nail head, you will drive it straighter and bend fewer nails.